ESP32 with DC Motor and L298N Motor Driver – Control Speed and Direction
This tutorial shows how to control the direction and speed of a DC motor using an ESP32 and the L298N Motor Driver. First, we’ll take a quick look on how the L298N motor driver works. Then, we’ll show you an example on how to control the speed and direction of a DC motor using the ESP32 with Arduino IDE and the L298N motor driver.

Note: there are many ways to control a DC motor. We’ll be using the L298N motor driver. This tutorial is also compatible with similar motor driver modules.
To better understand with this tutorial, you may want to take a look at the following posts:
- Getting Started with ESP32 Dev Module
- Installing the ESP32 Board in Arduino IDE (Windows instructions)
- Installing the ESP32 Board in Arduino IDE (Mac and Linux instructions)
- ESP32 Web Server – Arduino IDE
Parts Required
To complete this tutorial you need the following parts:

- ESP32 DOIT DEVKIT V1 Board – read ESP32 Development Boards Review and Comparison
- DC motor
- L298N motor driver
- Power source: 4x 1.5 AA batteries or Bench power supply
- 2x 100nF ceramic capacitors (optional)
- 1x SPDT slide switch (optional)
- Jumper wires
You can use the preceding links or go directly to MakerAdvisor.com/tools to find all the parts for your projects at the best price!
Introducing the L298N Motor Driver
There are many ways to control a DC motor. The method we’ll use here is suitable for most hobbyist motors, that require 6V or 12V to operate.
We’re going to use the L298N motor driver that can handle up to 3A at 35V. Additionally, it allows us to drive two DC motors simultaneously, which is perfect to build a robot.
The L298N motor driver is shown in the following figure:

L298N Motor Driver pinout
Let’s take a look at the L298N motor driver pinout and see how it works.

The motor driver has a two terminal block in each side for each motor. OUT1 and OUT2 at the left and OUT3 and OUT4 at the right.
- OUT1: DC motor A + terminal
- OUT2: DC motor A – terminal
- OUT3: DC motor B + terminal
- OUT4: DC motor B – terminal
At the bottom you have a three terminal block with +12V, GND, and +5V. The +12V terminal block is used to power up the motors. The +5V terminal is used to power up the L298N chip. However, if the jumper is in place, the chip is powered using the motor’s power supply and you don’t need to supply 5V through the +5V terminal.
Note: if you supply more than 12V, you need to remove the jumper and supply 5V to the +5V terminal.
It’s important to note that despite the +12V terminal name, with the setup we’ll use here (with the jumper in place) you can supply any voltage between 6V and 12V. In this tutorial will be using 4 AA 1.5V batteries that combined output approximately 6V, but you can use any other suitable power supply. For example, you can use a bench power supply to test this tutorial.
In summary:
- +12V: The +12V terminal is where you should connect your power supply
- GND: power supply GND
- +5V: provide 5V if jumper is removed. Acts as a 5V output if jumper is in place
- Jumper: jumper in place – uses the motors power supply to power up the chip. Jumper removed: you need to provide 5V to the +5V terminal. If you supply more than 12V, you should remove the jumper
At the bottom right you have four input pins and two enable terminals. The input pins are used to control the direction of your DC motors, and the enable pins are used to control the speed of each motor.
- IN1: Input 1 for Motor A
- IN2: Input 2 for Motor A
- IN3: Input 1 for Motor B
- IN4: Input 2 for Motor B
- EN1: Enable pin for Motor A
- EN2: Enable pin for Motor B
There are jumper caps on the enable pins by default. You need to remove those jumper caps to control the speed of your motors.
Control DC motors with the L298N
Now that you’re familiar with the L298N Motor Driver, let’s see how to use it to control your DC motors.
Enable pins
The enable pins are like an ON and OFF switch for your motors. For example:
- If you send a HIGH signal to the enable 1 pin, motor A is ready to be controlled and at the maximum speed;
- If you send a LOW signal to the enable 1 pin, motor A turns off;
- If you send a PWM signal, you can control the speed of the motor. The motor speed is proportional to the duty cycle. However, note that for small duty cycles, the motors might not spin, and make a continuous buzz sound.
SIGNAL ON THE ENABLE PIN | MOTOR STATE |
---|---|
HIGH | Motor enabled |
LOW | Motor not enabled |
PWM | Motor enabled: speed proportional to duty cycle |
Input pins
The input pins control the direction the motors are spinning. Input 1 and input 2 control motor A, and input 3 and 4 control motor B.
- If you apply LOW to input1 and HIGH to input 2, the motor will spin forward;
- If you apply power the other way around: HIGH to input 1 and LOW to input 2, the motor will rotate backwards. Motor B can be controlled using the same method but applying HIGH or LOW to input 3 and input 4.
Controlling 2 DC Motors – ideal to build a robot
If you want to build a robot car using 2 DC motors, these should be rotating in specific directions to make the robot go left, right, forward or backwards.
For example, if you want your robot to move forward, both motors should be rotating forward. To make it go backwards, both should be rotating backwards.
To turn the robot in one direction, you need to spin the opposite motor faster. For example, to make the robot turn right, enable the motor at the left, and disable the motor at the right. The following table shows the input pins’ state combinations for the robot directions.
DIRECTION | INPUT 1 | INPUT 2 | INPUT 3 | INPUT 4 |
---|---|---|---|---|
Forward | 0 | 1 | 0 | 1 |
Backward | 1 | 0 | 1 | 0 |
Right | 0 | 1 | 0 | 0 |
Left | 0 | 0 | 0 | 1 |
Stop | 0 | 0 | 0 | 0 |
Recommended reading: Build Robot Car Chassis Kit for ESP32, ESP8266, Arduino, etc…
Control DC Motor with ESP32 – Speed and Direction
Now that you know how to control a DC motor with the L298N motor driver, let’s build a simple example to control the speed and direction of one DC motor.
Schematic
The motor we’ll control is connected to the motor A output pins, so we need to wire the ENABLEA, INPUT1 and INPUT2 pins of the motor driver to the ESP32. Follow the next schematic diagram to wire the DC motor and the L298N motor driver to the ESP32.
The DC motor requires a big jump in current to move, so the motors should be powered using an external power source from the ESP32. As an example, we’re using 4AA batteries, but you can use any other suitable power supply. In this configuration, you can use a power supply with 6V to 12V.
The switch between the battery holder and the motor driver is optional, but it is very handy to cut and apply power. This way you don’t need to constantly connect and then disconnect the wires to save power.
We recommend soldering a 0.1uF ceramic capacitor to the positive and negative terminals of the DC motor, as shown in the diagram to help smooth out any voltage spikes. (Note: the motors also work without the capacitor.)
Preparing the Arduino IDE
There’s an add-on for the Arduino IDE allows you to program the ESP32 using the Arduino IDE and its programming language. Follow one of the next tutorials to prepare your Arduino IDE to work with the ESP32, if you haven’t already.
- Windows instructions – ESP32 Board in Arduino IDE
- Mac and Linux instructions – ESP32 Board in Arduino IDE
After making sure you have the ESP32 add-on installed, you can continue this tutorial.
Uploading code
The following code controls the speed and direction of the DC motor. This code is not useful in the real world, this is just a simple example to better understand how to control the speed and direction of a DC motor with the ESP32.
/*********
Rui Santos
Complete project details at https://randomnerdtutorials.com
*********/
// Motor A
int motor1Pin1 = 27;
int motor1Pin2 = 26;
int enable1Pin = 14;
// Setting PWM properties
const int freq = 30000;
const int pwmChannel = 0;
const int resolution = 8;
int dutyCycle = 200;
void setup() {
// sets the pins as outputs:
pinMode(motor1Pin1, OUTPUT);
pinMode(motor1Pin2, OUTPUT);
pinMode(enable1Pin, OUTPUT);
// configure LED PWM functionalitites
ledcSetup(pwmChannel, freq, resolution);
// attach the channel to the GPIO to be controlled
ledcAttachPin(enable1Pin, pwmChannel);
Serial.begin(115200);
// testing
Serial.print("Testing DC Motor...");
}
void loop() {
// Move the DC motor forward at maximum speed
Serial.println("Moving Forward");
digitalWrite(motor1Pin1, LOW);
digitalWrite(motor1Pin2, HIGH);
delay(2000);
// Stop the DC motor
Serial.println("Motor stopped");
digitalWrite(motor1Pin1, LOW);
digitalWrite(motor1Pin2, LOW);
delay(1000);
// Move DC motor backwards at maximum speed
Serial.println("Moving Backwards");
digitalWrite(motor1Pin1, HIGH);
digitalWrite(motor1Pin2, LOW);
delay(2000);
// Stop the DC motor
Serial.println("Motor stopped");
digitalWrite(motor1Pin1, LOW);
digitalWrite(motor1Pin2, LOW);
delay(1000);
// Move DC motor forward with increasing speed
digitalWrite(motor1Pin1, HIGH);
digitalWrite(motor1Pin2, LOW);
while (dutyCycle <= 255){
ledcWrite(pwmChannel, dutyCycle);
Serial.print("Forward with duty cycle: ");
Serial.println(dutyCycle);
dutyCycle = dutyCycle + 5;
delay(500);
}
dutyCycle = 200;
}
Upload the code to your ESP32. Make sure you have the right board and COM port selected. Let’s take a look on how the code works.
Declaring motor pins
First, you define the GPIOs the motor pins are connected to. In this case, Input 1 for motor A is connected to GPIO 27, the Input 2 to GPIO 26, and the Enable pin to GPIO 14.
int motor1Pin1 = 27;
int motor1Pin2 = 26;
int enable1Pin = 14;
Setting the PWM properties to control the speed
As we’ve seen previously, you can control the DC motor speed by applying a PWM signal to the enable pin of the L298N motor driver. The speed will be proportional to the duty cycle. To use PWM with the ESP32, you need to set the PWM signal properties first.
const int freq = 30000;
const int pwmChannel = 0;
const int resolution = 8;
int dutyCycle = 200;
In this case, we’re generating a signal of 30000 Hz on channel 0 with a 8-bit resolution. We start with a duty cycle of 200 (you can set a duty cycle value from 0 to 255).
For the frequency we’re using, when you apply duty cycles smaller than 200, the motor won’t move and will make a weird buzz sound. So, that’s why we set a duty cycle of 200 at the start.
Note: the PWM properties we’re defining here are just an example. The motor works fine with other frequencies.
setup()
In the setup(), you start by setting the motor pins as outputs.
pinMode(motor1Pin1, OUTPUT);
pinMode(motor1Pin2, OUTPUT);
pinMode(enable1Pin, OUTPUT);
You need to configure a PWM signal with the properties you’ve defined earlier by using the ledcSetup() function that accepts as arguments, the pwmChannel, the frequency, and the resolution, as follows:
ledcSetup(pwmChannel, freq, resolution);
Next, you need to choose the GPIO you’ll get the signal from. For that use the ledcAttachPin() function that accepts as arguments the GPIO where you want to get the signal, and the channel that is generating the signal. In this example, we’ll get the signal in the enable1Pin GPIO, that corresponds to GPIO 14. The channel that generates the signal is the pwmChannel, that corresponds to channel 0.
ledcAttachPin(enable1Pin, pwmChannel);
Moving the DC motor forward
In the loop() is where the motor moves. The code is well comment on what each part of the code does. To move the motor forward, you set input 1 pin to LOW and input 2 pint to HIGH. In this example, the motor speeds forward for 2 seconds (2000 milliseconds).
// Move the DC motor forward at maximum speed
Serial.println("Moving Forward");
digitalWrite(motor1Pin1, LOW);
digitalWrite(motor1Pin2, HIGH);
delay(2000);
Moving the DC motor backwards
To move the DC motor backwards you apply power to the motor input pins the other way around. HIGH to input 1 and LOW to input 2.
// Move DC motor backwards at maximum speed
Serial.println("Moving Backwards");
digitalWrite(motor1Pin1, HIGH);
digitalWrite(motor1Pin2, LOW);
delay(2000);
Stop the DC motor
To make the DC motor stop, you can either set the enable pin to LOW, or set both input 1 and input 2 pins to LOW. In this example we’re setting both input pins to LOW.
// Stop the DC motor
Serial.println("Motor stopped");
digitalWrite(motor1Pin1, LOW);
digitalWrite(motor1Pin2, LOW);
delay(1000);
Controlling the DC motor speed
To control the DC motor speed, we need to change the PWM signal duty cycle. For that you use the ledcWrite() function that accepts as arguments the PWM channel that is generating the signal (not the output GPIO) and the duty cycle, as follows.
ledcWrite(pwmChannel, dutyCycle);
In our example, we have a while loop that increases the duty cycle by 5 in every loop.
// Move DC motor forward with increasing speed
digitalWrite(motor1Pin1, HIGH);
digitalWrite(motor1Pin2, LOW);
while (dutyCycle <= 255){
ledcWrite(pwmChannel, dutyCycle);
Serial.print("Forward with duty cycle: ");
Serial.println(dutyCycle);
dutyCycle = dutyCycle + 5;
delay(500);
}
When the while condition is no longer true, we set the duty cycle to 200 again.
dutyCycle = 200;
Watch the Video Demonstration
Watch the next video to see the project in action:
Wrapping Up
In this tutorial we’ve shown you how to control the direction and speed of a DC motor using an ESP32 and the L298N motor driver. In summary:
- To control the direction the DC motor is spinning you use the input 1 and input 2 pins;
- Apply LOW to input 1 and HIGH to input 2 to spin the motor forward. Apply power the other way around to make it spin backwards;
- To control the speed of the DC motor, you use a PWM signal on the enable pin. The speed of the DC motor is proportional to the duty cycle.
We hope you’ve found this tutorial useful.
This is an excerpt from our course: Learn ESP32 with Arduino IDE. If you like ESP32 and you want to learn more about it, we recommend enrolling in Learn ESP32 with Arduino IDE course.
You might also like reading:
- Learn ESP32 with Arduino IDE
- ESP32 Servo Motor Web Server with Arduino IDE
- Alexa (Echo) with ESP32 and ESP8266 – Voice Controlled Relay
- Build an All-in-One ESP32 Weather Station Shield
- ESP32 Publish Sensor Readings to Google Sheets
Thanks for reading.
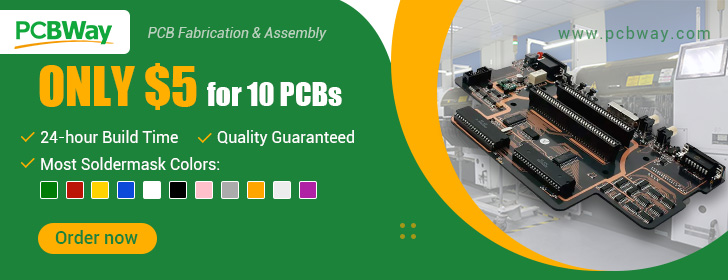
Couldn’t you use two PWM channels to drive the H-bridges? Should give you smoother control.
Hi Alan.
Yes, you can use two PWM channels. For example, one controls one motor, and the other channel the other motor.
Or you can use the same PWM channel for both motors if you want them to have a similar behavior.
this is my program to control two motors, i use L293D motor driver, but the motor couldn’t spin in the same time. the first motor spin and stop, then the second motor start and not stop, please help me how to spin motor in the same time. im sorry for my bad english.
{
digitalWrite(leftForward,HIGH);
digitalWrite(leftBackward,LOW);
digitalWrite(rightForward,HIGH);
digitalWrite(rightBackward,LOW);
while (dutyCycle <= 255){
ledcWrite(ledChannel1, dutyCycle);
ledcWrite(ledChannel2, dutyCycle);
dutyCycle = dutyCycle + 5;
delay(500);
}
dutyCycle = 100;
}
Hi Evan.
Change one of the motors red wire with the black wire, when connecting to L293D motor driver.
For example, connect motor A red wire to OUT2 and the black wire to OUT1, and see what you get.
I hope this helps.
Regards
Sara
Please tell me the code you are using it does not look like Arduino C+?
Thanks, Bob
Hi, how do i set a 16bit resolution to drive two motors, how do I decide the frequency?
Hello Surya,
You can set the bit resolution in your sketch in that line:
const int resolution = 8;
I recommend trying different frequencies and read the datasheet for your particular motor to find the best frequency. With these types of motors we usually use a frequency between 2000-40000 Hz
I hope this helps. Regards,
Rui
Hi, I can’t figure out how to PWM modulate speed on 2 channels. Whatever I tried, only one channel changes speed.
I’m copying samples of my sketch below, knowing that I’m only asking if according to you this should work and, if not, why. It’s kinda frustrating to be back to square one with ESP32! lol
Thanks in advance.
Here is the code I’m using:
[code]
// Setting PWM properties
const int freq = 40000;
const int pwmChannelL = 0;
const int pwmChannelR = 1;
const int resolution = 8;
(…)
// configure LED PWM functionalitites
ledcSetup(pwmChannelL, freq, resolution);
ledcSetup(pwmChannelR, freq, resolution);
// attach the channel to the GPIO to be controlled
ledcAttachPin(ENABLE_LEFT, pwmChannelL);
ledcAttachPin(ENABLE_RIGHT, pwmChannelR);
(…)
int dutcycl = SLOW; // sartpoint
if (SpeedReqST > reqSpeed) { // if ST requested a speed greater than the last one registered by fwd() or here
while (dutcycl <= SpeedReqST) {
ledcWrite(pwmChannelL, dutcycl);
ledcWrite(pwmChannelR, dutcycl);
// Serial.print("Forward with duty cycle: ");
// Serial.println(dutcycl);
dutcycl += 1;
delay(100);
}
}
else if (SpeedReqST = SpeedReqST) {
ledcWrite(pwmChannelL, dutcycl);
ledcWrite(pwmChannelR, dutcycl);
// Serial.print(“Forward with duty cycle: “);
// Serial.println(dutcycl);
dutcycl -= 1;
delay(100);
}
}
// update last value
reqSpeed = SpeedReqST;
[/code]
Hi.
Which GPIOs are you using to control the motors? Make sure you are not using “Input only GPIOs”.
If you want both motors to have the same behavior, you can attach both enable pins to the same channel. Then, you just need to control one channel and both motors will work similarly.
Regards,
Sara
Thank you for your answer! Actually it was a problem with my encoders management code, which was systematically reducing pwm on one channel, continuously… pure coding mistake, in a library I had forgotten to correct… :p
Thanks again Sara.
many many thanks fpr the great tutorial – would love to see a port to mycropython . d o you thnk taht this is possible
love to hear from you
greetings
Hi Martin.
What do you mean by “port to micropython”?
We’re working on a tutorial for the L298N with ESP8266 and ESP32 with MicroPython.
It is not published yet, but it will be published soon.
Regards,
Sara
Hi which pin of esp32 can be connected to motor driver if we use two motor (Motor A&B)? I tried to connect many pin of esp32 for two motor but doesn’t work.how to code PWM
to control two motor?
Hi Tracy.
Any output pin of the ESP32 can connect to the motor driver (except input-only pins). Read the GPIO reference guide for more information: https://randomnerdtutorials.com/esp32-pinout-reference-gpios/
You can connect the following pins, for example:
IN1: GPIO27
IN2: GPIO 26
ENA (enable pin for motor A): GPIO 14
IN3: GPIO 33
IN4: GPIO 25
ENB (enable pin for motor B): GPIO 32
To learn more about PWM with the ESP32, you can read the following tutorial: https://randomnerdtutorials.com/esp32-pwm-arduino-ide/
I hope this helps.
Regards,
Sara
Thanks Sara
Hey tracy you succeed move 2 dc motor?
Hi Sara,
I tried with this modified code below but only my left motor works . There is no movement in my right motor. Is that any problem in my code? Can help?
// Motor A
int LM1 = 27;
int LM2 = 26;
int ENA = 14;
//Motor B
int RM1 = 33;
int RM2 = 25;
int ENB= 32;
// Setting PWM properties
const int freq = 30000;
const int pwmChannelLM = 0;
const int pwmChannelRM = 1;
const int resolution = 8;
int dutyCycle = 200;
void setup() {
// sets the pins as outputs:
pinMode(LM1, OUTPUT);
pinMode(LM2, OUTPUT);
pinMode(ENA, OUTPUT);
pinMode(RM1, OUTPUT);
pinMode(RM2, OUTPUT);
pinMode(ENB, OUTPUT);
// configure LED PWM functionalitites
ledcSetup(pwmChannelLM, freq, resolution);
ledcSetup(pwmChannelRM, freq, resolution);
// attach the channel to the GPIO to be controlled
ledcAttachPin(ENA, pwmChannelLM);
ledcAttachPin(ENB, pwmChannelRM);
Serial.begin(115200);
// testing
Serial.print(“Testing DC Motor…”);
}
void loop() {
// Move the DC motor forward at maximum speed
Serial.println(“Moving Forward”);
digitalWrite(LM1, LOW);
digitalWrite(LM2, HIGH);
digitalWrite(RM1, LOW);
digitalWrite(RM2, HIGH);
delay(2000);
// Stop the DC motor
Serial.println(“Motor stopped”);
digitalWrite(LM1, LOW);
digitalWrite(LM2, LOW);
digitalWrite(RM1, LOW);
digitalWrite(RM2, LOW);
delay(1000);
// Move DC motor backwards at maximum speed
Serial.println(“Moving Backwards”);
digitalWrite(LM1, HIGH);
digitalWrite(LM2, LOW);
digitalWrite(RM1, HIGH);
digitalWrite(RM2, LOW);
delay(2000);
// Stop the DC motor
Serial.println(“Motor stopped”);
digitalWrite(LM1, LOW);
digitalWrite(LM2, LOW);
digitalWrite(RM1, LOW);
digitalWrite(RM2, LOW);
delay(1000);
// Move DC motor forward with increasing speed
digitalWrite(LM1, HIGH);
digitalWrite(LM2, LOW);
digitalWrite(RM1, HIGH);
digitalWrite(RM2, LOW);
while (dutyCycle <= 255){
ledcWrite(pwmChannelLM, dutyCycle);
ledcWrite(pwmChannelRM, dutyCycle);
Serial.print("Forward with duty cycle: ");
Serial.println(dutyCycle);
dutyCycle = dutyCycle + 5;
delay(500);
}
dutyCycle = 200;
}
Dear Tray,
I used your code on other pins of the ESP32.
Needless to say, it worked and thanks to you my project has movement.
I searched earth and land for a code that did this.
I also edited it having two dutyCycles (CycleA and B) to have each motor work at a different speed.
Thank you so much.
Hola intente mesclar el proyecto de los leds por servidor wiffi y el este y que mi carro no andaba y crei que era porque el codigo no tiene el PWM y este si pero me arroja error-
CODIGO:
#include
const char* ssid = “CowBoy”;
const char* password = “GATOSxGATOS”;
WiFiServer server(80);
String header;
…
}
Hi Martin.
What error do you get?
Can you copy the error?
Next time try to post your question in English so that our readers can understand.
Regards,
Sara
Sara what frequency for 100 duty cycle
You should be able to leave the same frequency
Hi,
Do you have a micropython example?
Hi.
At the moment, we don’t have any MicroPpython tutorial about this subject.
However, it can be easily adapted to MicroPython if you know how to use PWM.
You can follow the next tutorial: https://randomnerdtutorials.com/esp32-esp8266-pwm-micropython/
Regards,
Sara
Is there a way have the battery pack also power the esp32?
That way I just flip the on switch and every is working from one power source instead of USB and double A batteries
ssue: unable to flash micropython to esp 32: open serial error, please try again. hope to connect internet and try again.
pretty new to micropython – want to flash micropython to esp 32 ( resp 8266) board.
Quote
getting this errors all the time.
open serial error, please try again.
hope to connect internet and try again.
current version only open py txt json ini file.
hope to connect internet and try again.
hope to connect internet and try again.
any idea;
many thanks for any and all help in advance.
Hi Martin.
Next time, please try to post your question in the right blog post. This article is not related with MicroPython.
I recommend flashing micropython firmware using esptool: https://randomnerdtutorials.com/flashing-micropython-firmware-esptool-py-esp32-esp8266/
Then, I recommend using Thonny as you IDE: https://randomnerdtutorials.com/getting-started-thonny-micropython-python-ide-esp32-esp8266/
I hope this helps.
Regards,
Sara
What happens if one wants to drive a 1.5v / 3v motor?
Much below the 6v lower limit for the L298?
You have to use pwm signal in order to reduce the frequency or the motor will die soon if receives 6v constantly
Hi! thank you for your tutorial
Quote: “For the frequency we’re using, when you apply duty cycles smaller than 200, the motor won’t move and will make a weird buzz sound”
How can this be avoided? because if the resolution allows values beteween 0 and 255, by starting at 200 we lose 78% of the values and the motor is much less controllable!!
Thank you
Hello,
I am having some trouble getting my motors to spin with my ESP32 and the L298N. I believe I have narrowed down the problem to the voltage that the ESP32 is supplying to the L298N’s input pins.
Using a multimeter, I am reading an expected 3.2v when I use digitalWrite() to the ESP32’s output pin. However, when it’s attached to the motor’s input pin on the L298N, nothing happens. When I supply 5v to the input pin, the motor moves.
From the L298N’s datasheet, I see that the input voltage is from -0.3 – 7v. Would you know why my ESP32’s 3.2 is failing to drive the motor?
Thank you!
Hey guys, the L298N is ancient, dont use it.
Why? it’s literally back from 1980s.
– it needs 3 GPIOs for one motor, wtf?! (wtf= what for?)
– it uses old transistors, loosing a lot of energy (draining your batteries and reducing max voltage significantly)
– it puts that energy into heat (needing to be cooled)
– so it has a big heatsink (making that board giantic overall)
I dropped dead when i received those monsters, they are bigger than my ESP board.
I reccomend the adarfruit drv8871: can handle more Amperes, less hot, much smaller, needs 2 wires per motor, still cheap. Done.
I checked L298 spec sheet, that its nominal input voltage is 5V, but esp32 out put is only 3.3V. That means for 12V power supply we provide 10V something to motors?
Hello,
I’m trying to follow this tutorial, I did everything step-by-step, cabling everything as shown and using the same exact code.
There are 2 differences in my experiment, I’m using a 7.4V battery to power the L298N and I’m using a different motor. My motor is one of those 6V yellow motors used by robot car kits.
My problem is that it only rotates only if motor1Pin1 is set to LOW and motor1Pin2 is set to HIGH (forward direction), not if they are set opposite (backward).
I’ve connected the L298N to Arduino and the motor can rotate forward and backward.
What problem could I have with this tutorial?
Hey can i use this method – L298N for a 3.7v pump If so what are the changes
Hello,
I’m trying to use the tutorial sketch with an H brigde L193D.
One thing seems odd.
At startup, the Forward, Stopped and Backward sequences do not work. They execute only after running the Forward increase sequence. After that the sketch runs normally. Do you have any idea what the problem could be.
Thanks for your help.
Hello
It isn’t a L193D but a L293D
Reg
output of l298n is 2.5V??? I want to increase its base output voltage 3-5V to drive the motor faster?
Hello,
I don’t find much information about the frequency setting
“const int freq = XXX”
I see examples that put 40Khz and other 1Khz for very similar DC motors. Yet something will change ..
Doing some tests with the classic yellow motors for arduino I noticed that by putting a lower frequency (700 hz) the dutycicle also works at values below 100 (with 8bit = 0/255) but using 2 motors it seems to me that are more evident some speed differences between motors, while at high frequencies the motors run at equal speed.
Anyone have similar experiences?
Are there any reference parameters to choose the right frequency for different actuators?
and again …
Does the frequency value affect the motor torque?
On my side it is not working. I have removed the jumpers but no rotation
One of the shortfalls of using the L298N board is that it doesn’t use the sense pins on the L298N chip. One needs to use the bare L298N chip in order to access them. The purpose of those pins is to measure the current drawn by each motor through a shunt resistor. If you connect the hot side of that resistor to an analog input of the ESP32, you can verify that the motor is consuming the correct amount of current. No current could mean that te motor is not spinning for some reason (like a bad connection or broken motor coil), too much current would mean that the motor can’t cope with the load or is even stalling.
The only limitation is that the voltage drop across the shunt resistor must not exceed 2V (I assume that he voltage drop is at the expense of Vgs to drive the lower leg of the H-bridge).
You’re using a way too high frequency. I tell you why. Moving my experimental robot driven by two geared 12V/0,58A DC motors from an Uno to an ESP32, I had to change the PWM-part of my code and I set the PWM-frequency at 10 kHz. This resulted in motors that would hardly move if the duty cycle was reduced to about 50% and didn’t move at all for lower duty cycles. Since the default PWM frequency of an Uno is 490 Hz, I lowered it to this value. After that my motors were driving as I was used to.
Choosing a very high frequency reduces the transferred energy to the motor immense. A normal DC motor is, seen from the electronical point of view, a slow device. Compare it with a potter’s wheel of which you control the speed by giving it a firm kick once a while. Imagine the ineffectiveness to softly kick it ten times a second.
I believe it’s reasonless to choose a PWM frequency higher than about 1000 Hz for any motor whatsoever.
Hi.
Thanks for the advice.
I have to try this with a lower frequency.
Regards,
Sara
Hey Rui and Sara,
Thanks so much for this tutorial! BTW, I just used the code with an ESP32-S3 DevKitC-1 board, and the only changes required were the motor pin numbers. Unless I’m missing something, pins 26 and 27 aren’t exposed on this board. I used 12 and 13 instead, and the code worked like a charm.
Steve
That’s great!
Thanks for sharing your feedback.
Regards,
Sara